Introduction to Load Cycles
The term “load cycle” in the context of modern cranes describes the fluctuations and dynamic loads affecting the crane and its components. Applications such as pile driving or the use of vibrating equipment (e.g., vibratory hammers) can generate vibrations, leading to continuous alternations between load and relief. Without suitable measures, these cyclic stresses can cause premature wear, material fatigue, or even cracks in the crane structure. Therefore, measures such as using vibration dampers are essential to minimize load cycles, ensuring both safety and longevity of the crane.
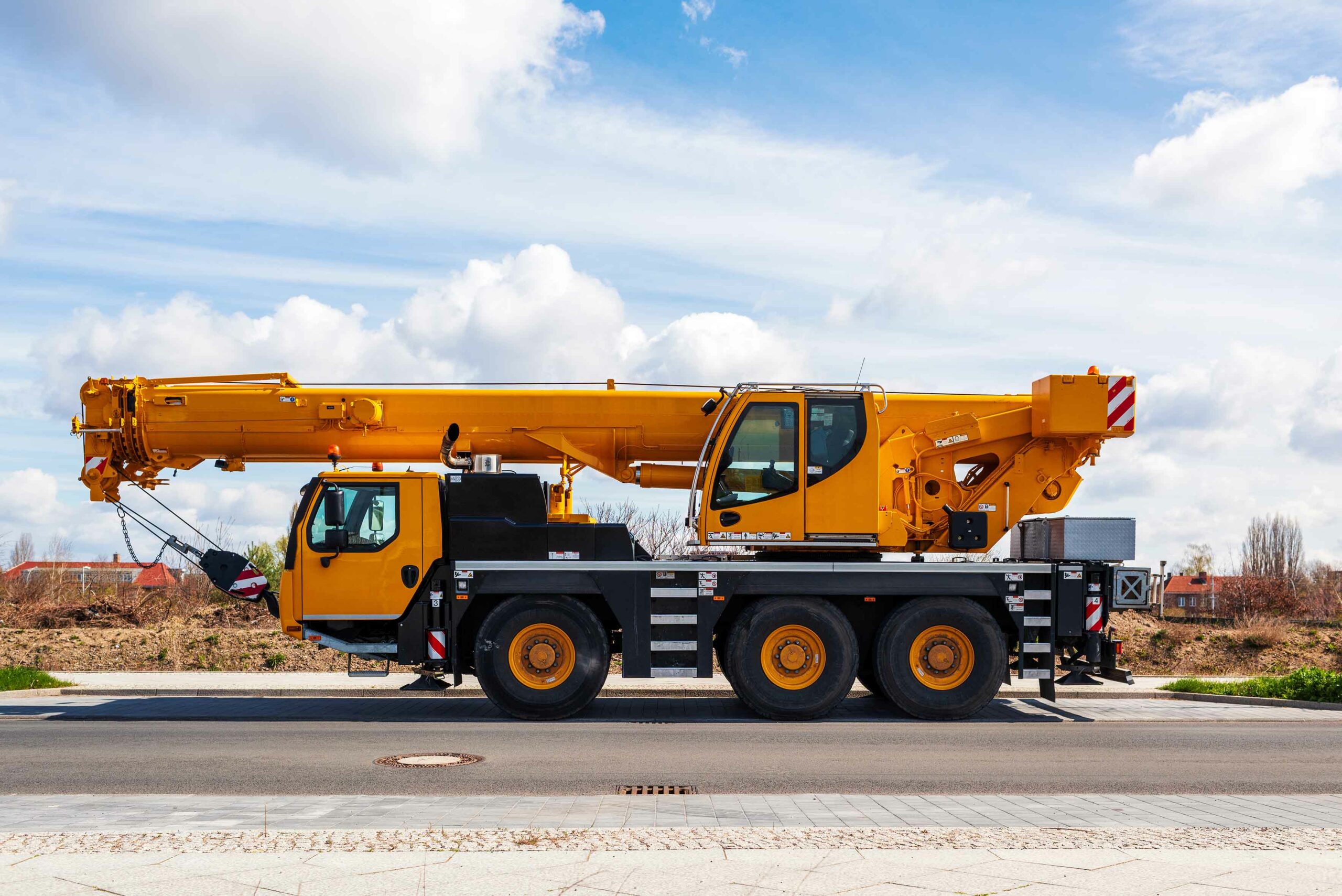
Significance of Load Cycles in BS EN 13001
BS EN 13001 focuses extensively on load cycles and their impact on the durability and fatigue strength of cranes. It addresses load cycles in terms of fatigue stress and load classification. Key points include:
- Definition of Load Collectives and Cycles: The standard specifies how various loads on the crane are calculated and evaluated, differentiating between static and dynamic cycles and defining load collectives relevant to different crane types and operating conditions.
- Classification of Duty Groups: Cranes are categorized into duty groups based on the frequency and intensity of load cycles, enabling customization to specific requirements, such as infrequent heavy lifts or frequent light lifts.
- Fatigue Analysis Based on Load Cycles: The standard provides methods to calculate the crane structure’s fatigue life, with load cycles as a critical factor, predicting cumulative load impacts over time.
- Consideration of Load Cycles for Individual Components: Components subject to frequent load cycles, such as welds and bolted joints, must demonstrate high fatigue resistance.
- Combination of Load Cycles with Safety Factors: To account for uncertainties, the standard requires safety factors based on load cycles.
- Maximum Allowable Cycles to Prevent Fatigue Failure: BS EN 13001 gives guidelines for the maximum number of load cycles to prevent fatigue failure, especially for high-cycle components.
Classification of Load Types According to BS EN 13001
The standard categorizes several load types to systematize operational stresses:
- Static Load: Constant forces, such as the crane’s weight, act on the structure continuously, influencing basic component design.
- Dynamic Load: This includes forces from crane movements, accelerations, decelerations, and shocks, often inducing temporary, significant forces.
- Fatigue Load: Cyclic stresses from repeated load cycles can lead to long-term structural damage. The standard outlines methods for calculating fatigue life and limiting allowable cycles.
- High Safety Requirements: Rare but extreme conditions, like emergency stops or wind gusts, are accounted for with safety factors to ensure safe crane operation in exceptional situations.
- Environmental Loads: Factors like wind, temperature, and corrosion impact durability and load-bearing capacity.
- Buckling Loads: Slender crane components, such as booms, may face instability risks under compression, necessitating stability calculations.
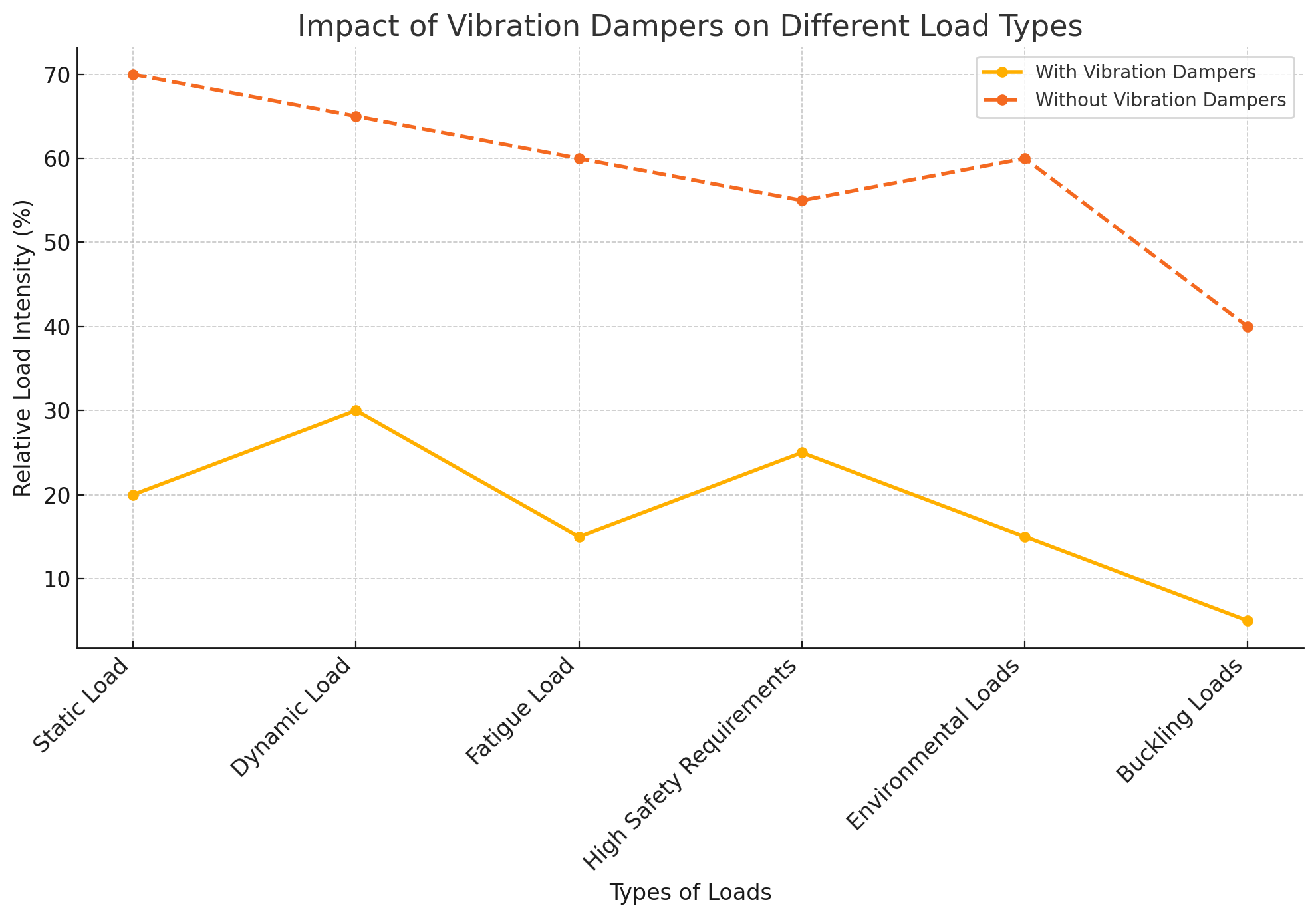
Comparing Load Types Across Crane Applications
Heavy lifting imposes intermittent loads with variable cycles, generally less frequent, while pile driving with vibratory hammers exerts continuous, high-frequency vibrations, intensifying fatigue stress. Vibration dampers are crucial here, reducing high-frequency oscillations and lowering fatigue risks.
Impact of Using Vibration Dampers
Vibration dampers provide considerable benefits in pile-driving operations:
- Reduction of Peak Loads and Cyclic Stresses: Dampers isolate vibrational energy, reducing load peaks and cycle amplitudes by up to 90%.
- Extended Structural Life: Reduced vibrations lower fatigue, extending component and structural life, and maintenance intervals.
- Operational Stability and Safety: Lower vibration transfer results in greater operational stability and safety.
- Inspection and Maintenance Requirements: Reduced cyclic loads decrease maintenance needs, allowing parts replacement within standard cycles.
- Lifetime Cost Comparison: Dampers initially add cost but reduce long-term wear, repair frequency, and maintenance, lowering overall costs.
Reducing load cycles and using vibration dampers in pile-driving operations are essential for modern crane safety and longevity. By adhering to BS EN 13001, crane operators can increase operational safety and lower lifetime costs.
When using modern cranes for piling work, it is recommended to use vibration dampers between the hook and the vibration hammer to minimise damage caused by vibrations.
Do you want to increase the safety and efficiency of your crane fleet? Contact us today to learn more about our certified shock dampers. Together, we can ensure a safer and more sustainable future for the crane and construction industry!
Contact us to find out more about our shock absorbers and to optimally protect your machines.